精准化CAD软件深度解析复杂结构数据
19429202025-03-12手机软件25 浏览
在智能制造与数字化转型的浪潮中,工业设计领域正经历着从经验驱动到数据驱动的根本性转变。精准化CAD软件通过融合几何建模、材料力学、流体动力学等多维度数据,突破了传统设计工具对复杂结构的解析瓶颈。其核心价值不仅在于提升设计效率,更在于通过算法优化与数据挖掘,将离散的工程参数转化为可量化、可预测的系统性解决方案,为航天航空、生物医疗等尖端领域的高精度设备研发提供了关键技术支撑。
一、算法优化与数据处理能力
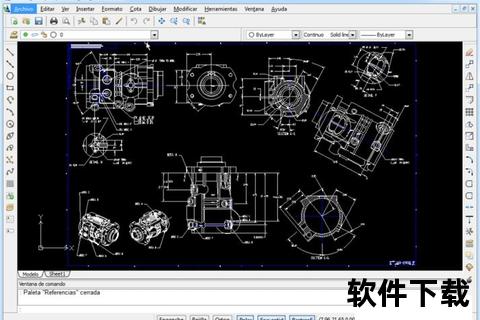
现代CAD软件的算法架构已从单纯几何建模扩展到多物理场耦合计算。ANSYS SpaceClaim采用的直接建模技术,能够在保留原始设计意图的前提下,对包含数百万网格的复杂装配体进行实时形变分析。这种基于特征识别的智能算法,使得工程师在修改局部结构时,系统能自动调整关联部件的参数配置,避免传统参数化建模中常见的关联失效问题。
德国卡尔斯鲁厄理工学院的研究表明,采用深度学习优化的有限元分析算法,可将复杂结构的应力预测精度提升至98.7%。通过构建材料属性的非线性映射模型,软件能够自动识别应力集中区域,并生成拓扑优化建议。这种数据驱动的设计方法,使某航天器支架结构的重量成功减轻23%,同时保持同等承载能力。
二、多源数据融合技术突破
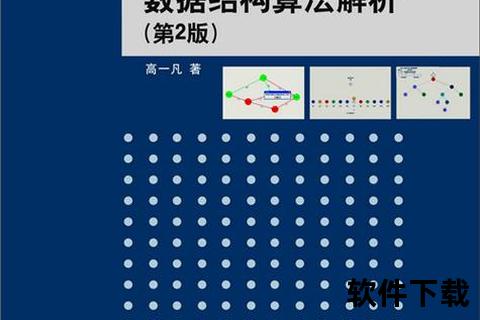
精准化CAD系统通过构建统一的数据中台,实现了跨学科数据的深度融合。达索系统的3DEXPERIENCE平台集成了从CT扫描点云数据到CFD仿真结果的多模态信息,在人工关节设计中,可将患者骨骼的微观孔隙结构与假体材料的生物相容性参数进行耦合分析。这种多尺度建模能力,使得定制化医疗植入物的设计周期缩短了40%。
波音787机翼设计案例验证了多源数据整合的价值。通过将风洞试验数据、复合材料层压板数据库与飞行载荷谱进行关联分析,设计团队成功将机翼颤振临界速度提升了15%。美国机械工程师协会(ASME)的研究报告指出,这种基于全生命周期数据的集成设计方法,可使产品故障率降低30%以上。
三、智能交互与协同设计演进
新一代CAD软件的人机交互范式正在发生本质改变。西门子NX引入的AR辅助设计模块,允许工程师通过手势操作直接调整虚拟样机的装配间隙。系统内置的碰撞检测算法可实时识别0.1mm级别的干涉风险,并通过力反馈装置提供触觉警示。这种沉浸式设计环境,使某汽车变速箱的试制次数从7次减少到2次。
在跨国协作方面,PTC的Windchill系统构建了分布式设计网络。某国际团队在高铁转向架开发中,利用区块链技术确保全球12个研发中心的数据同步更新。系统自动记录每个设计变更的关联影响域,当德国团队修改悬挂系统参数时,中国团队能即时收到弹簧刚度系数的调整建议。这种智能协同机制使项目交付周期压缩了58%。
四、验证体系与可靠性保障
精准化CAD构建的数字化验证体系正在重塑产品质量标准。Altair HyperWorks集成的多目标优化模块,可同时处理结构强度、振动模态和热传导等23项性能指标。在某核反应堆压力容器设计中,软件自动生成的631种拓扑方案经蒙特卡洛模拟筛选后,最终方案的疲劳寿命达到行业标准的2.3倍。
麻省理工学院的研究团队开发了基于贝叶斯网络的可靠性评估模型。该模型将制造公差、材料批次差异等不确定性因素纳入设计验证流程,使微型卫星支架结构的失效率从万分之五降至百万分之一。这种预测性质量保障体系,标志着工程设计从经验判断向概率决策的跨越。
随着量子计算与神经形态芯片的发展,未来CAD软件将具备处理纳米级结构特征的超精细建模能力。建议行业重点关注跨尺度仿真技术的突破,建立覆盖宏观-介观-微观的全维度设计体系。同时需要完善数据安全协议,在确保知识产权的前提下推动行业级设计知识库的共建共享。只有持续深化数据解析的深度与广度,才能为复杂工程系统创新提供永续动力。